What is Porosity in Welding: Recognizing Its Reasons and Enhancing Your Skills
What is Porosity in Welding: Recognizing Its Reasons and Enhancing Your Skills
Blog Article
Porosity in Welding: Identifying Common Issues and Implementing Best Practices for Prevention
Porosity in welding is a prevalent issue that commonly goes undetected until it causes substantial problems with the stability of welds. This typical problem can endanger the toughness and longevity of bonded structures, presenting safety and security risks and leading to expensive rework. By recognizing the source of porosity and applying reliable avoidance approaches, welders can dramatically improve the high quality and dependability of their welds. In this discussion, we will check out the crucial elements contributing to porosity formation, analyze its destructive results on weld efficiency, and talk about the most effective practices that can be adopted to decrease porosity event in welding processes.
Typical Sources Of Porosity

One more frequent culprit behind porosity is the existence of pollutants on the surface of the base steel, such as oil, grease, or corrosion. When these pollutants are not properly eliminated before welding, they can vaporize and come to be caught in the weld, creating flaws. Making use of dirty or wet filler products can introduce contaminations into the weld, contributing to porosity concerns. To reduce these common root causes of porosity, comprehensive cleaning of base steels, proper protecting gas option, and adherence to optimum welding parameters are vital techniques in achieving premium, porosity-free welds.
Influence of Porosity on Weld Quality

The existence of porosity in welding can dramatically compromise the structural stability and mechanical residential properties of bonded joints. Porosity develops gaps within the weld steel, deteriorating its overall toughness and load-bearing ability. These voids act as stress focus points, making the weld more susceptible to fracturing and failure under used tons. Furthermore, porosity can decrease the weld's resistance to rust and other environmental variables, better lessening its long life and efficiency.
Welds with high porosity degrees tend to display reduced effect toughness and decreased capacity to warp plastically before fracturing. Porosity can impede the weld's ability to properly transmit forces, leading to premature weld failing and potential security threats in vital frameworks.
Best Practices for Porosity Avoidance
To enhance the structural honesty and quality of welded joints, what certain measures can be carried out to decrease the occurrence of porosity during the welding procedure? Porosity avoidance in welding is important to make certain the integrity and strength of the final weld. One reliable technique appertains cleaning of the base steel, getting rid of any pollutants such as corrosion, oil, paint, or dampness that can lead to gas entrapment. Making sure that the welding tools remains in good condition, with clean consumables and proper gas circulation prices, can additionally significantly decrease porosity. Furthermore, keeping a secure arc and regulating the welding parameters, such as voltage, current, and take a trip rate, helps create a consistent weld pool that lessens the threat of gas entrapment. Using the correct welding strategy for the details product being bonded, such as readjusting the welding angle and weapon placement, can better prevent porosity. Regular inspection of welds and immediate remediation of any issues recognized throughout the welding procedure are crucial techniques to protect against porosity and generate high-quality welds.
Significance of Proper Welding Strategies
Carrying out proper welding strategies is vital in guaranteeing the architectural stability and quality of bonded joints, building on the foundation of reliable porosity prevention actions. Welding methods directly influence the overall toughness and sturdiness of the welded structure. One vital facet of proper welding methods is preserving the appropriate heat input. Extreme heat can cause enhanced porosity as a result of the entrapment of gases in the weld pool. Alternatively, insufficient warmth may lead to incomplete fusion, developing prospective weak points in look at these guys the joint. Furthermore, using the ideal welding specifications, such as voltage, present, and take a trip rate, is crucial for accomplishing audio welds with very little porosity.
In addition, the selection of welding procedure, whether it be MIG, TIG, or stick welding, need to line up with the details requirements of the task to ensure optimum outcomes. Appropriate cleaning and prep work of the base metal, along with picking the ideal filler product, are additionally necessary parts of efficient welding techniques. By adhering to these ideal practices, welders can reduce the risk of porosity formation and create top notch, structurally sound welds.
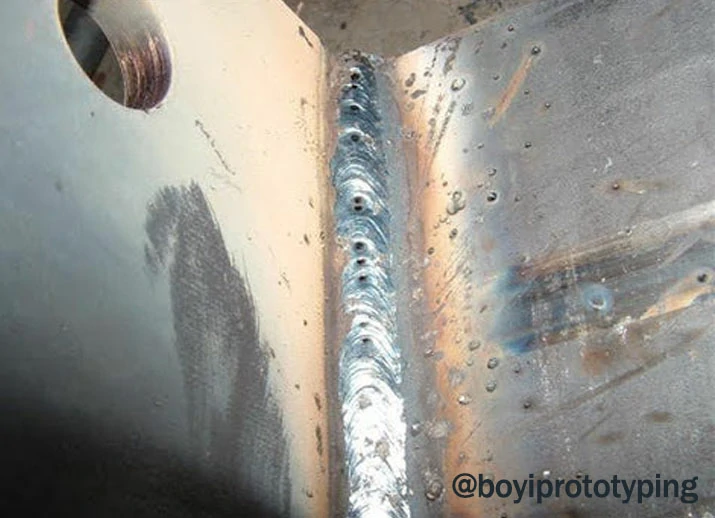
Evaluating and Quality Assurance Actions
Quality assurance actions play a critical function in validating the stability go and integrity of bonded joints. Examining procedures are necessary to detect and avoid porosity in welding, ensuring the toughness and toughness of the last product. Non-destructive screening approaches such as ultrasonic testing, radiographic screening, and visual examination are frequently employed to identify prospective flaws like porosity. These strategies enable the analysis of weld top quality without endangering the honesty of the joint. What is Porosity.
Performing pre-weld and post-weld assessments is likewise critical in keeping high quality control standards. Pre-weld examinations include verifying the products, devices setups, and tidiness of the work location to avoid contamination. Post-weld inspections, on the various other hand, assess the last weld for any issues, including porosity, and validate that it satisfies defined standards. Applying an extensive top quality control plan that consists have a peek here of comprehensive screening procedures and examinations is critical to lowering porosity concerns and guaranteeing the general top quality of bonded joints.
Final Thought
To conclude, porosity in welding can be a common issue that influences the top quality of welds. By identifying the common root causes of porosity and carrying out ideal practices for prevention, such as appropriate welding strategies and testing measures, welders can guarantee premium quality and trusted welds. It is important to prioritize prevention techniques to lessen the event of porosity and keep the honesty of bonded frameworks.
Report this page